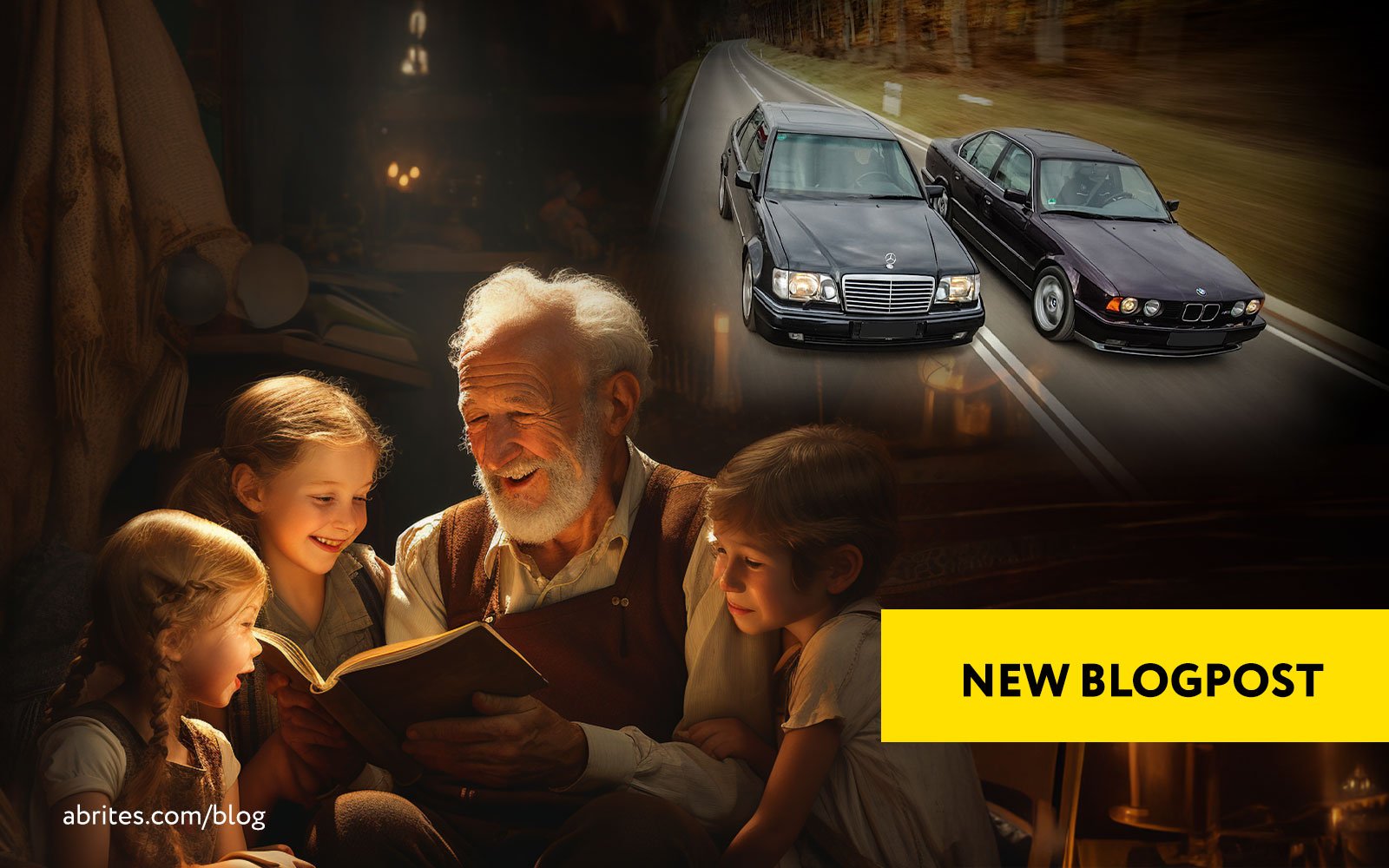
How Does Electronic Fuel Injection Work
I sometimes imagine myself as an old man, sitting in front of my future house – slightly overlooking the barn, where I have my car collection. I imagine having grandchildren and when my grandchildren inevitably make the fatal error of asking me: “Grandpa, what were internal combustion cars like?” I would say “Sit down, little one, let me tell you a story better than anything Disney or Pixar could ever butcher. Today, my dear reader – you have the ill fate of playing the role of my grandchildren.
I love cars, I always have. I believe them to be among the greatest inventions of mankind. I also believe that the most awe-inspiring part of the vehicle to most people is the internal combustion engine. We all know them – from the one cylinder bike engines like the Yamaha Aerox to the Bugatti Tourbillon’s W16 – they are “in essence” all the same, some simpler, others more complex but at their core they are all the same – there is a cylinder, inside this cylinder is a piston, the piston is connected to a rod, cleverly named the “connecting rod” which is connected to a shaft that cranks once again wittily named the “crankshaft” which transfers the up- down motion of the piston to a rotating motion which makes the car go vroom. This is the piston engine – developed by many people but was patented by Nicolaus August Otto. After Otto’s initial after several years of development the four-stroke internal combustion piston engine was born. It is the most common version you will see in modern vehicles.
In order to understand the idea of the electronic fuel injection you must first know the four strokes of the internal combustion.
These are:
- Intake (Piston goes down, it intakes the air/fuel mixture. Intake valves let it through)
- Compression (Piston goes up, it compresses the combustible mixture both valves are closed to create pressure)
- Power (The spark plug ignites this mixture, forcing the piston down)
- Exhaust (Piston is still down, exhaust valves open and the burnt mixture evacuates from the compression chamber)
This simple, yet brilliant cycle repeats many times and depending on the configuration of the engine different pistons are always in different states of it thus causing a constant crankshaft motion. There is a cheeky colloquial term for the four-stroke combustion cycle known as “SUCK, SQUISH, BANG, BLOW”, which is easier to remember. Injection two types of injection – port injection is when the fuel is sprayed on the back side of the valve and is mixed with the incoming air before it reaches the combustion chamber, but nowadays those are all but gone. Nowadays manufacturers prefer direct injection, where the fuel is sprayed directly into the chamber. This allows much more precise control of the fuel mixture, higher pressure for better atomization of the fuel and is generally much more efficient. Below you can find the graph of the different positions of the pistons as well as an example of port vs. direct injection. However, you want to place these pistons - 90 °, 60°, 180° or anything in between – this is how it all works in a four-stroke piston engine with however many cylinders you want to put.
There are also Wankel rotary engines, named after its creator - Felix Heinrich Wankel. Mr. Wankel was a pioneer but what he created wasn’t really a good one. I know that there are many RX-7 and RX-8 fanboys who swear by their rotary, but they are just very high maintenance, short lasting, inefficient engines and unless turbocharged below 5000rpm. Sorry, Mazda boys. Anyway, Mazda was not the only manufacturer to adopt the rotary. NSU had a go in the RO-80, designed by Klaus Luthe. The 3.5 stroke engine as I like to call it relies on a triangular shaped object, rotating in a Minion shaped casing with three ports. I hope the graphic below explains. If you need details on EFI in rotary – write me an email and I will make a blog post but just for you.
No story about the internal combustion engine will ever be worth its weight unless you put the following sentence in it: Internal Combustion Engines (ICE) are nothing more than an air pump. There, I said it. I believe the author of this iconic statement is A. Graham Bell, he is the man responsible for much of my education. I have most of his books and will list most of them below. Now back to the story…
As early as the 1950s people much smarter than me started realizing that carburetors are absolutely useless. They then started playing around with mechanical injections, the first of its kind was the 300SL Mercedes- Benz. Later, around the 1970s people started creating more complex computing technology which allowed much more precise control over the air/fuel mixture. This is when Electronic Fuel Injection became a thing. It took off because cars were much more efficient, they became just as good at sea level as in the Andes and a new standard was created. Let’s jump forward a few years and start the actual talk about the EFI.
I will now tell you more about the components and functionality of the EFI systems.
Why did I waste 8 minutes of your time telling you the above? – In order to understand EFI we need to know that there are 4 things to control as per the four cycles – we need to know how much air is coming into the engine to control the suck stroke, we need to know when to spray the fuel, we need to know when to ignite the mixture and we need to know when to open and close the valves. This is what in engineering terms is called timing. Clever people do not come up with innovative names, what their inventions do is usually what it says on the tin. Now timing is usually referred to the valve work – when the valves open and when they shut, both intake and exhaust. At this point we have another engineering term we need to discuss. This is the position of piston number one (whichever number one is in the configuration). There we need to find the Top Dead Center (TDC). The TDC is the absolute highest point which the piston will reach in the cylinder. Everything in modern ICEs is measured from there- the position of the camshafts which open the valves, the firing of the spark plug, the spraying of the injectors – all of that. Now today we have a few ways of measuring TDC – usually it is done by the so called “missing tooth” method – a simple, yet brutally effective method which allows you to have a plate on the crankshaft on the outside of the engine block which has teeth, (picture a sprocket) but one of those teeth is missing. The crankshaft positioning timing gear is keyed to the crankshaft, meaning it can only be mounted one way. This ensures that you cannot go wrong with it. So, this gear has many teeth but one of them is missing. Once this one is missing manufacturers put an electromagnetic (Hall type after its inventor) sensor near the gear.
Every time the missing tooth passes by the sensor (Crankshaft Positioning Sensor) we know that that is our TDC. This is measured between idle and the max revolutions of the crankshaft in RPM or revolutions per minute, so up to 20,000RPM in the highest revving engines. Based on this sensor we know when we can time the firing of the air/fuel mixture and the opening and closing of the valves. In the olden days the firing of the spark plugs in order was dictated by the distributor (a basic metal arm rotating in the order inside a plastic container touching other metal bits to conduct electricity) which distributed electrical impulses to each plug at the predetermined order according to the crankshaft position, the timing belt, chain or gears were permanently timed to TDC. This means that under any external conditions (atmospheric pressure, temperature and moisture of the air we had exactly the same inputs of the engine, which basically meant that we had no influence over the engine to respond to external conditions. Nowadays with the evolution of EFI and the immense leap in computing technology we can have a lot of influence over the behavior of an engine in order to deliver the same performance when the air is cold and dense at sea level as well as when it is hot and humid in Kito, Peru for example. This is done by having a precise measurement of the incoming air for starters, we used to have a MAF (Mass Airflow Meter) with a hot wire in it, when the air would come into the engine the Engine Control Unit (ECU) would calculate how much the air cooled the hot wire which would give it the result of how much volume of air has entered the intake, it would then divide this volume into the number of cylinders and would estimate the amount of fuel needed to spray per cylinder, per ignition cycle in order to achieve stoichiometry (Lambda) which in the internal combustion engine is referred to as 14.7:1 meaning that for every 14.7 parts air we need to add 1 part fuel. Lambda is the perfect ratio of burning almost to completion of the fuel you are spraying; this means that the engine is most efficient when working at stoichiometric values. This is then measured by the “Lambda sensor” placed in the exhaust of the vehicle and corrections would be made constantly, multiple times per second. When we break it down like that it does not seem that difficult, does it? Now, today we very rarely see the exact version of this method. The reason for this is that we have a lot better technology. Today we have ECUs that could do absolutely everything necessary to make an engine run as efficiently as possible. We have individual coils (coils replaced the distributors and are electronically controlled to ignite each spark plug at a precise moment). Individual coils allow nanoseconds control over the exact point of spark. Sometimes before TDC, sometimes after, this is called advance and retard, in the olden days advance and retard of the spark was controlled by slight rotation of the cap of the distributor. Nowadays we can program that into the ECU, but moreover we can program a logic. So, what is this logic? Well, the quality of air coming in, its amount and humidity dictate basically the performance – if there is less air in the combustion chamber, we will have more fuel than the lambda ratio – this mixture is called a “rich” mixture, if there is less fuel and more air- the mixture is called a “lean” mixture. Depending on what the mixture is the ECU may choose to retard or advance the timing in order to burn most efficiently. This means that we will prevent a burning which is too cold, too hot, too lean, or too rich, this protects our engine and avoids detonations. But, grandpa, I hear you say – isn’t each cycle a detonation? It is, but if the piston is on its way up towards TDC and we ignite the mixture we will create a counter action, this counter action is the wrong kind of detonation and will eventually melt your piston or turn your crankshaft bearing into minced meat which both result in catastrophic engine failure over time, or immediately. For this reason, engines are equipped with knock sensors – the knock affectionately refers to the unwanted detonation described above. The knock sensor is essentially an electronic stethoscope “listening” for irregular detonation in the cylinders. Once it “hears” knock it sends this information to the ECU which can choose to retard timing, or in the case of modern engines even switch the cylinder off all together. Protection is just as important in modern electronic fuel injection as efficiency and performance. This is why modern EFI can basically sense everything and put the engine in limp mode whenever this is necessary to preserve the health of your engine. But wait, we spoke about timing, spark, air but what we are missing is the “F” part of EFI – FUEL. This is delivered to the combustion chamber via fuel injectors – those are extremely advanced since the initial mechanical fuel injector. Modern injectors allow complete control – they can port injectors – where the fuel is sprayed on the outside of the combustion chamber, direct injection, where the fuel is sprayed directly into the combustion chamber, you can have multiple injectors per cylinder, as well as multiple spark plugs to maximize efficiency. You can have high impedance fuel injectors when you want lower amounts of fuel to be sprayed in a more “misty” pattern, or low impedance injectors where you want larger amounts of fuel to be “dumped” into the chamber of secrets – anything you need can be achieved. Modern EFI is perfectly tailored and can allow you to make improvements. Depending on the situation and performance you can achieve great things. Most modern engines worth discussing are turbocharged, which allows many modifications but in any case – using EFI you (or your inputs to the ECU) can manage absolutely everything – if a fuel injector in a turbocharged car can come out of the factory flowing at only 60%, this will allow you to tell it to increase to 70%, increase the boost pressure slightly, adjust timing slightly to compensate and increase performance, you can turn cylinders off to increase fuel efficiency, you can set thresholds for control, you can have a sensor in the fuel line telling you what quality of fuel you have and adjust everything to ensure safety, you can also have cam control gears with multiple cam lobes to open or close the valves more or less depending on RPM and performance needs, you can have an electronically controlled throttle pedal to cruise or, control and operate. Anything you like, ah, such great times, kids. Of course, nowadays you have a set of soulless electric motors with potentiometers on them which make a G class turn on the spot, a Taycan accelerate from 0-100km/h in 2 seconds and mobile fridges with a “T” badge on to bring you to work. Where is my M119 V8, where is my S38B36? – In the barn, grandpa, God, you’re annoying.
Until next time, try to have fun at work.
Alek
I would like to thank:
- A. Graham Bell
- Charles White
- Jeff Hartman
- Ivaylo Drumev
- Ivan Krastev
For being my teachers into the world of EFI and diagnostics. The first three have about 15-20 books which will let you learn a lot more about EFI than I have summarized here as it barely scratches the surface, I did not get into MAP (Manifold absolute pressure), how the lambda measures the oxygen level in the exhaust gas to determine the ratio, how to tune for VO (volumetric efficiency), diesels, rotaries, and many others, I hope to do a follow up because a blog post is not meant to be 3000 words long, anyways. I will have an article on diagnosing EFI problems ASAP.